Belt Filer Press
The belt filter press is an environmental protection device that dewaters the mud through physical extrusion between the machine mesh belts.
The sludge first mixes and reacts with the flocculant and flocculates into a mass, and then passes through the pre-dehydration zone → concentration and dehydration zone → low-pressure drainage.
Zone → S-shaped extrusion zone → high pressure zone, so that the sludge water is gradually discharged through the mesh belt through the extrusion force between the mesh belts, and finally forms a mud cake to discharge.
Scope of application: Ceramics, metallurgical mines, coal washing, textile printing and dyeing, municipal sewage, papermaking, petrochemical, leather, brewing, food processing, chemical, pharmaceutical, electroplating and other industries.
PRODUCT INTRODUCTION
Belt filter press is an environmental protection device that dewaters mud through physical extrusion between belt belts on the machine. Sludge is mixed with flocculant to react and flocculate into lumps, and then passes through pre-dewatering area → concentration dewatering area → low pressure drainage area → S-shaped extrusion area → high pressure area so that sludge moisture is gradually discharged through the belt through the extrusion force between belt belts and finally discharged into mud cake.
SCOPE OF APPLICATION
Ceramics, metallurgical mines, coal washing, textile printing and dyeing, municipal sewage, paper making, petrochemical, leather,brewing, food processing, chemistry, pharmacy, electroplating and other industries.
DEHYDRATION PRINCIPLE
Ceramics, metallurgical mines, coal washing, textile printing and dyeing, municipal sewage, paper making, petrochemical, leather,brewing, food processing, chemistry, pharmacy, electroplating and other industries.
DEHYDRATION PROCESS
Sludge from different industries needs to use different kinds od flocculants, and the input amount is about 0.05% – 0.1%. According to different sludge characteristicsm, we will design and issue targeted programs and suppoting process flow to meet customer requirements.
MAIN FEATURES
- Modular structure design
- Continuous and automatic operation
- Stable and reliable pneumatic bias adjustment and bracing system.
- Low energy consumption, low cost operation and maintenance
- Maximize protection against corrosion and rust.
- Safe and clean operating environment.
- High efficiency dehydration performance.
TECHNICAL PARAMETERS

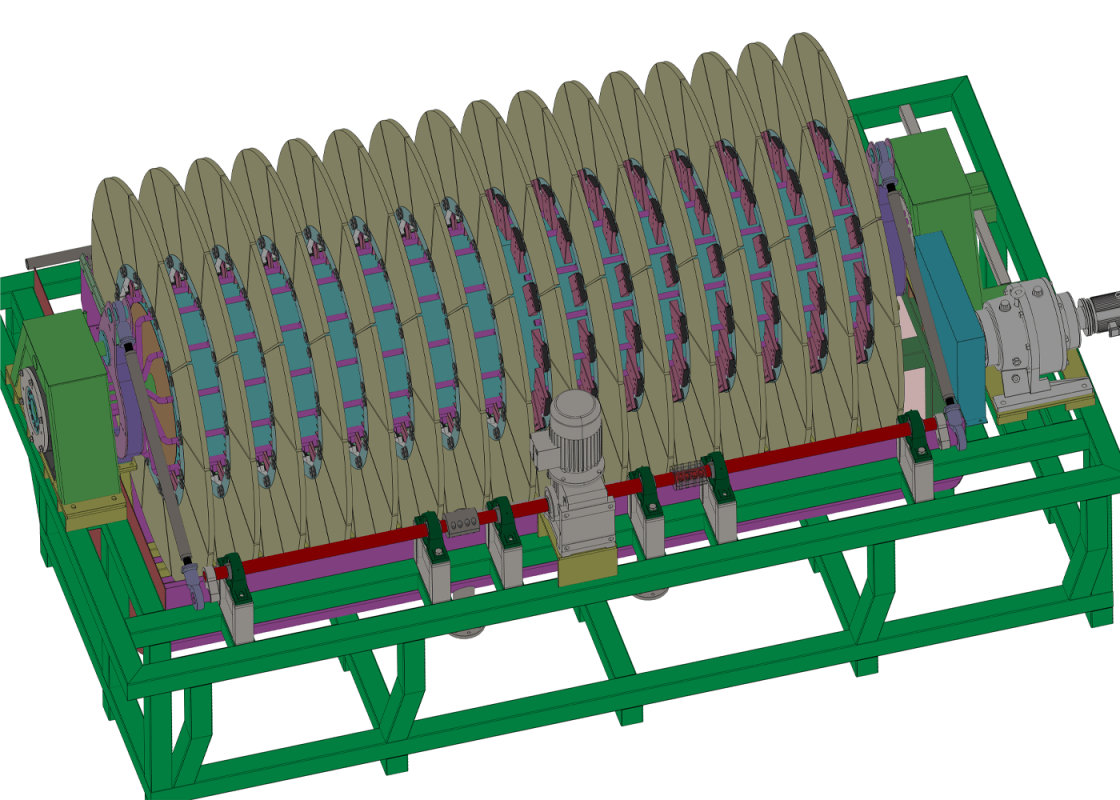
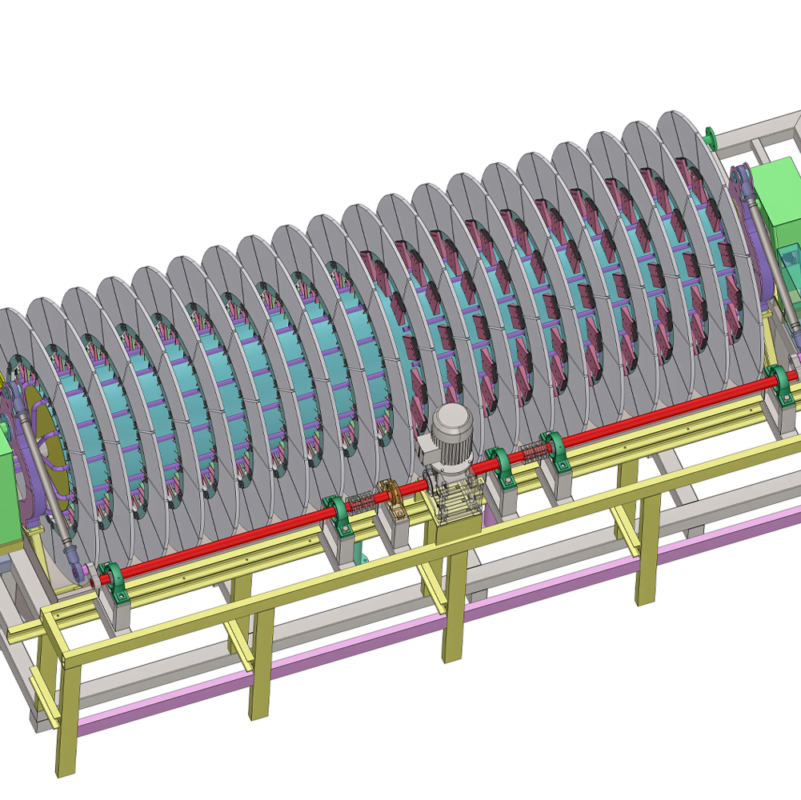
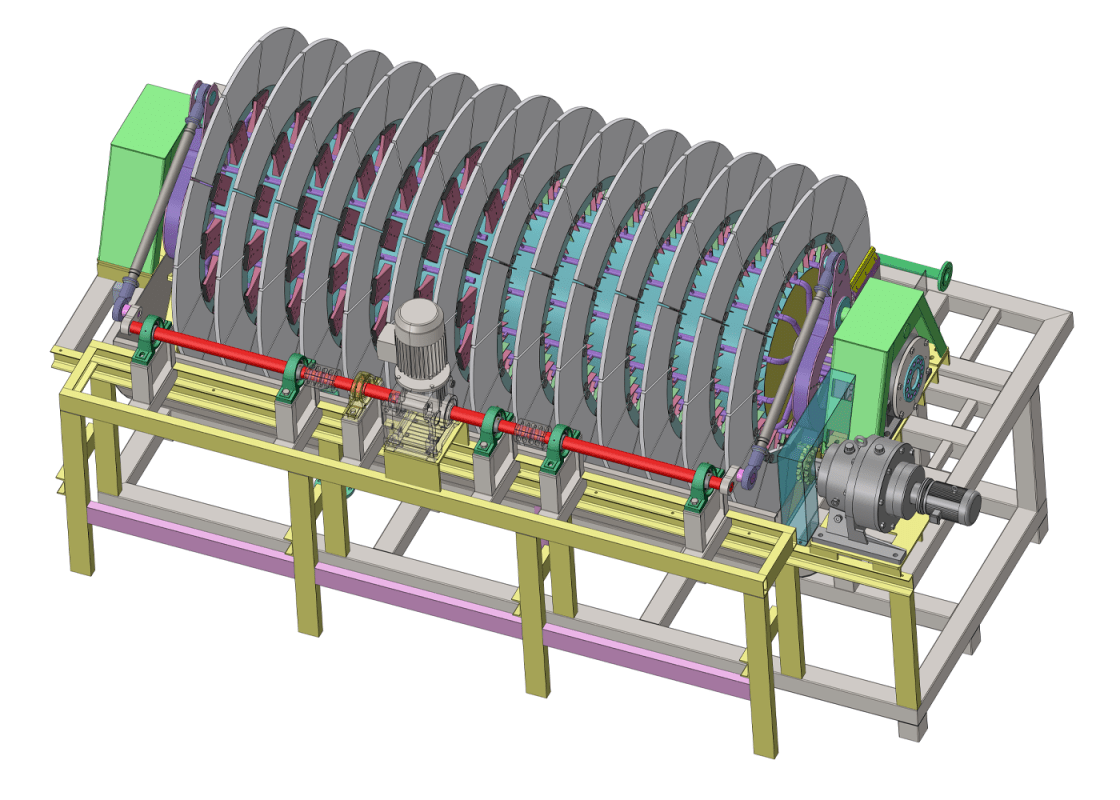
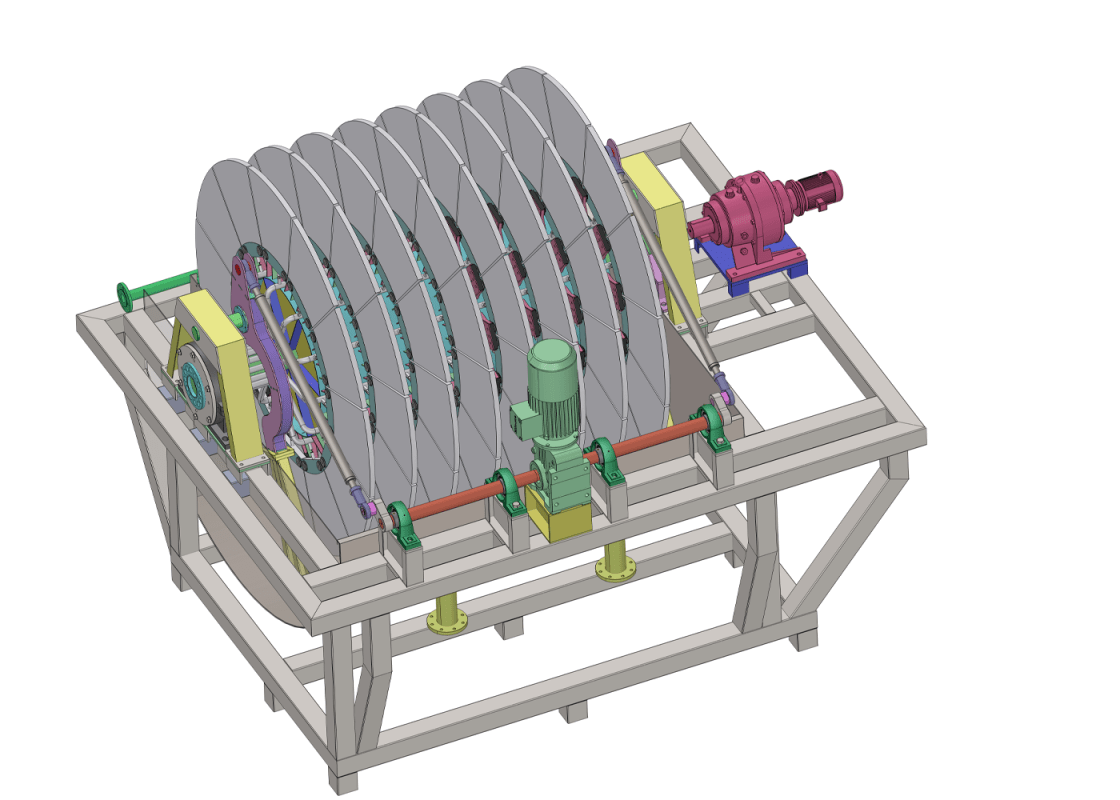
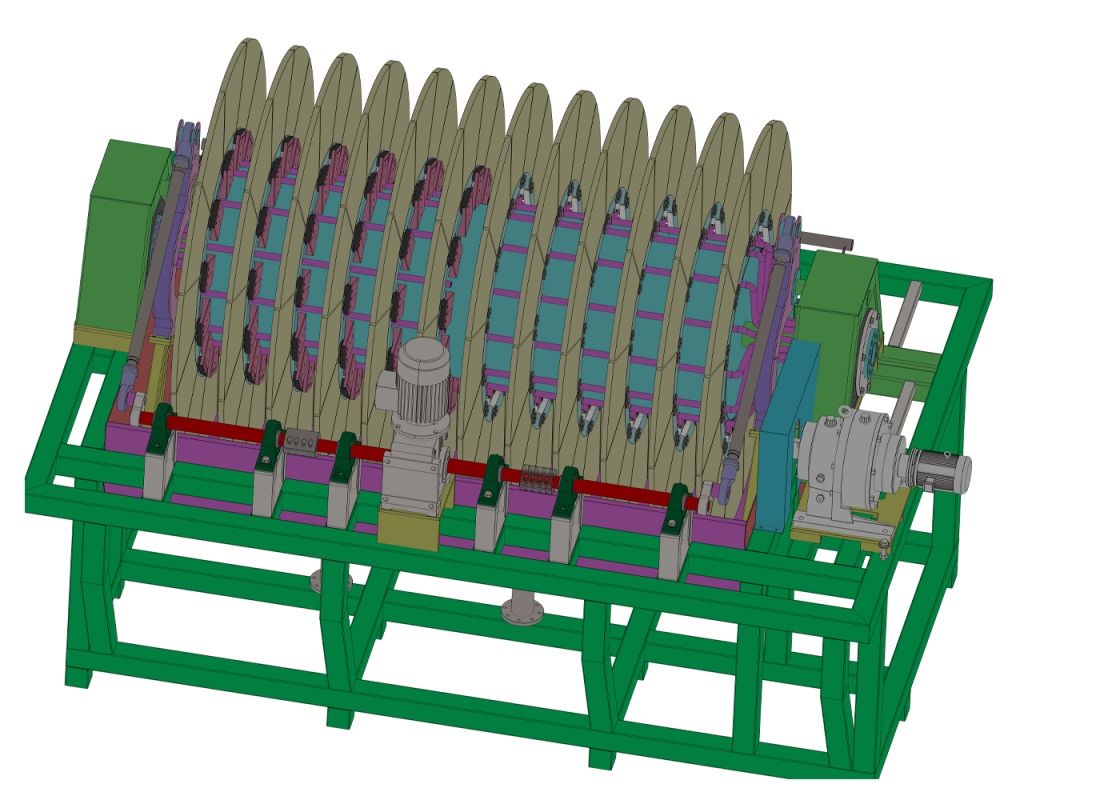